12 Jun DyStar’s Latest Breakthrough in yarn and piece dyeing with RotaSpray
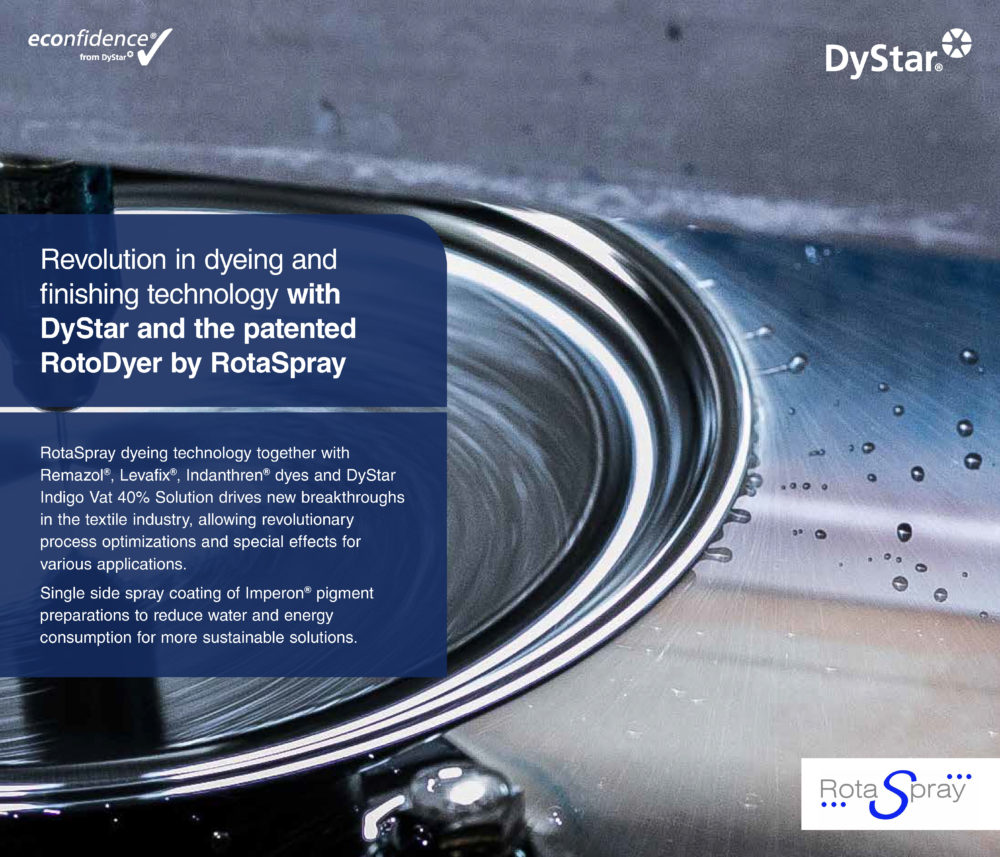
At DyStar, we are continuously searching for better ways in textile coloration. We not only limit ourselves to our own products. We always think outside the box to improve the application of our products as well. On that journey, we are working together with customers, machinery partners, brands and retailers to improve existing, or to develop new application technics for our dyes and auxiliaries.
Last year we achieved a real breakthrough in the Textile Industry together with our partner RotaSpray in yarn and piece dyeing: The newly developed DENIM Spray-Application-Technology for continuous yarn and fabric dyeing with DyStar® Indigo Vat 40% Solution, Cassulfon®, Remazol®, Levafix®, Indanthren® and Imperon® dyes and selected Sera® process auxiliaries.
What is so special about that?
A common problem in the Denim warp yarn dyeing process is the application of other dyes besides Indigo and sulphur dyes. The classical dipping bath application of conventional Indigo dyeing machines has been a major limitation so far in terms of shade continuity and reproducibility. The new Spray – Ox” and “Pad-Spray-Steam”- or as we call it “PS2” process, has succeeded in pushing these boundaries aside.
In combination with selected dyes and auxiliaries from DyStar, this technology allows a previously unknown variety of colours in the continuous dyeing of warp yarns, especially on small lots. Any mixtures of Indigo, sulphur and vat dyes can now be applied in one step, without fearing the well-known differences in affinity and exhaustion behaviours of dye mixtures. Contamination problems in Bottoming and Topping processes are eliminated.
A further breakthrough was achieved in the field of continuous yarn and fabric dyeing with reactive and vat dyes. The elimination of classical padders and large dipping baths is a revolution in our industry. The contactless application avoids contamination between the dye liquor and the chemical liquor. Hence, undesired hydrolysis of the reactive dyes no longer takes place. An intermediate drying, as in Pad-Dry-Pad-Steam process is obsolete. Nishat Mills has reported a reduction of 1.331 tons CO2 in 2019 by using PS2 process. It also allows a significant reduction of salt in dark colours, up to complete elimination in bright colours. This process reduces the environmental footprint of reactive dyeing significantly and it opens the door for Denim producers for a wider range of colour shades in short lots.
Existing slasher dyeing ranges can be expanded as a retrofit solution with the new spray dyeing process from RotaSpray. This has already been implied at pioneers of the denim industry such as Mou Fung (Hong Kong/China), Orta (Turkey), Arvind (India), Artistic Fabric Mills (Pakistan) and at Nishat Mills (Pakistan) for continuous fabric dyeing.
New compact slasher machine concepts based on this new application technology, are in planning. Let’s write the textbooks new with this disruptive technology!
For more information, drop us an enquiry here:
www.dystar.com/contact-dystar/